Not every bulk bag discharger is the same, so if you’re looking to expand or improve your bulk bag unloading line, keep this in mind. Companies that make use of bulk bags will need to upgrade and expand their unloading lines at some point, whether it’s to meet higher demands, improve efficiency or purchase new equipment.
Ultimately, this guide will guarantee that you make well-informed choices and choose customised solutions that fulfil your needs. You may attain accuracy, safety and efficiency in your bulk bag handling operations while saving time and money by using the appropriate unloading equipment.
Custom Bulk Bags is a leading manufacturer and supplier of bulk bags in South Africa. We produce up to 3.5 million bulk bags per year. Our products can safely hold between 500kg and two tonnes of material per bag, depending on your specifications.
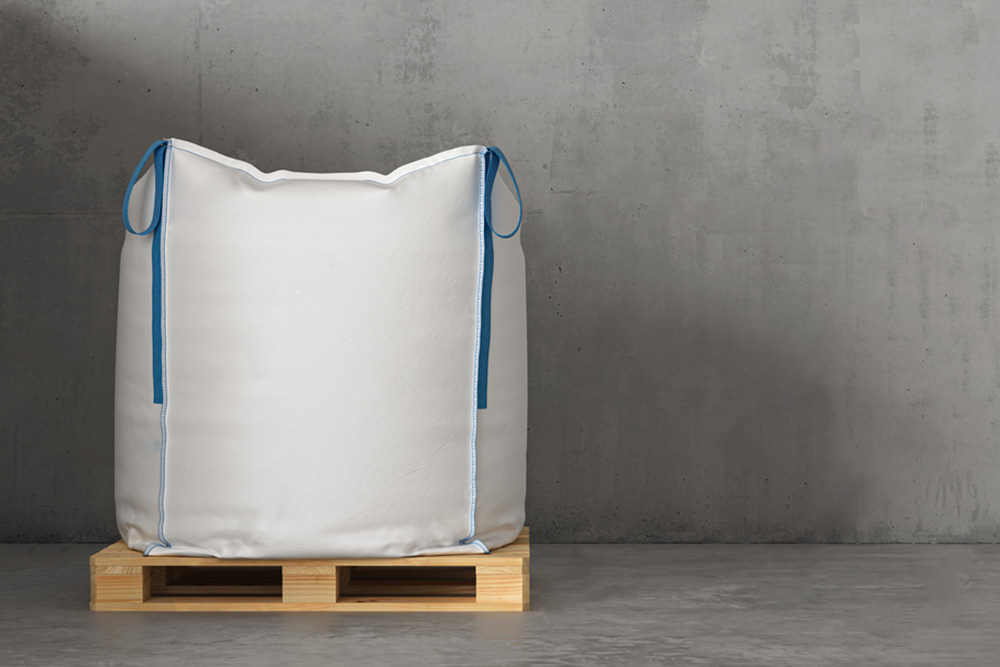
Define your unloading requirements
Start by assessing the materials, processes and bag requirements before diving into the finer points of bulk bag unloader customisation. You need to be clear on what type of material you’re discharging, what types of bulk bags you’ll be using (including their optional extras) and what unloading equipment you’d prefer to use.
The following points will help you make an informed decision:
- What are the features of the material and its flow characteristics?
- What kind and size of bags will be used?
- How will the baggage be handled (hoist or forklift)?
- Are there restrictions on headroom and space?
- Are there any weighing and batching specifications?
- How will bulk bags be removed and discarded?
- Are there any dust containment and hygiene requirements?
Understanding these requirements will paint a clear picture of what unloading equipment you need, whether it’s manual, semi- or fully-automated.

Design your bulk bags to meet your requirements
Custom Bulk Bags produces bespoke bulk bags for customers throughout South Africa. We provide free consultations with our customers to fully understand their unique needs and what they’d like to achieve through their bulk packaging. This allows us to design the perfect packaging solutions that fit their equipment.
When it comes to discharging bulk bags, there are various ways of doing so, such as full bottom discharge or spout discharge. Decide on what specifications you need and bring us a list of your requirements. These should include the following:
- Bulk bag dimensions and volume.
- Type and length of lifting loops.
- Sealing requirements.
- Base construction.
- Bottom discharge requirements (flat, conical, spout etc.).
We need to know how the bulk bags will be fed into the unloading equipment as this will determine the type and size of the lifting loops and other specifications. If your company uses forklifts or motorised hoists and trolleys, then this will determine various specs that need to be included on the bulk bags.
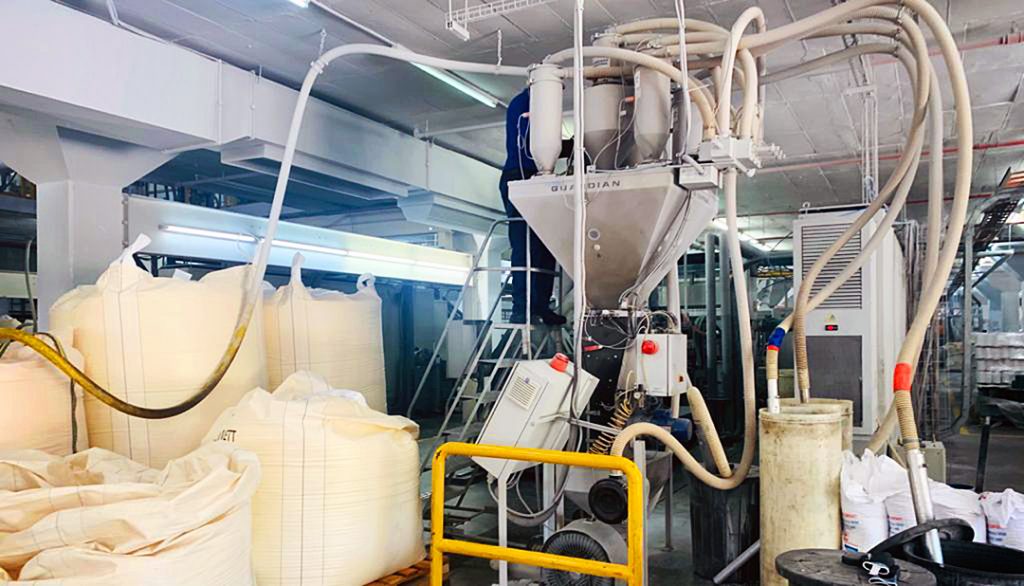
Downstream material transfer
Once your bulk bags have been discharged, how will the material travel downstream? The two most common solutions are gravity-fed and conveyor-fed systems. With gravity-fed systems, the material can be discharged through a hopper and allowed to fall freely into the designated container.
With a conveyor-fed system, the material is transported using a mechanical or pneumatic conveyor. This means that a full-bottom discharge bulk bag will not be suitable; rather a conical bottom should be included in the design specs. Understanding the downstream equipment will also determine what unloading equipment you will need to purchase.
Understand your weight batching requirements
In a bulk bag unloading process, weight batching or dosing are important considerations. These processes meter the material to provide an accurate weight or volume and can be done in two ways – loss-in-weight (LIW) or gain-in-weight (GIW). LIW requires that the bulk bag, discharger and metering device are weighed. The loss in weight is monitored and the discharge is stopped once the bulk bag loses a certain weight of material.
Alternatively, a GIW process monitors the weight of the downstream container that is being fed by the unloading equipment. When the container reaches a specific weight, the discharge is stopped. Both of these systems are accurate but you need to decide which method will work best for your unloading needs.
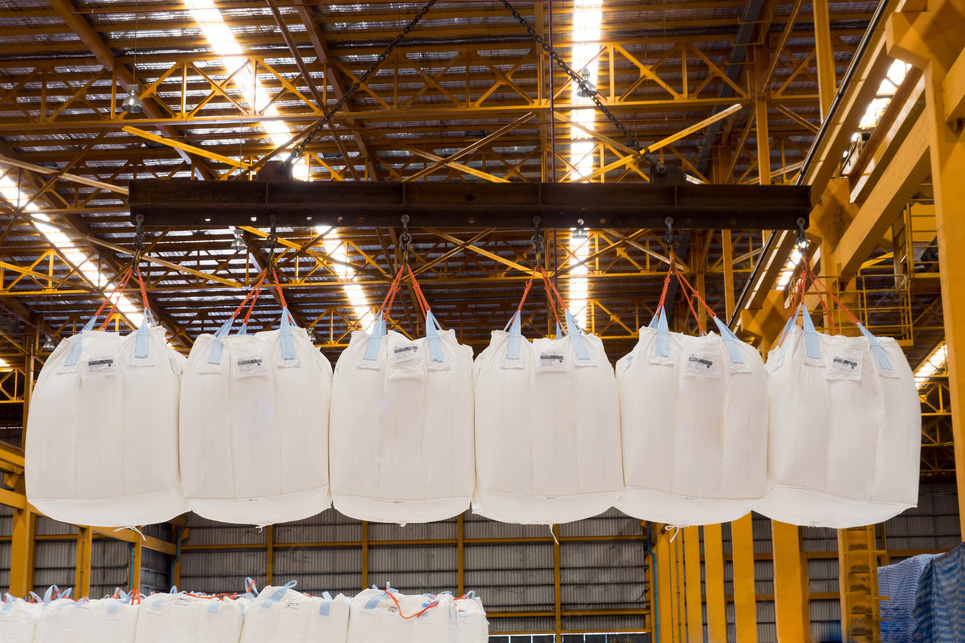
Testing your unloading equipment
Once you’ve decided on the best unloading equipment and it has been installed, you will need to test the system and make adjustments to ensure that it works optimally, efficiently and safely. Each component will need to be monitored closely and small changes can be made to ensure that your unloading line is accurate and working as it should.
Working with a reliable bulk bag manufacturer will eliminate any issues caused by bags that do not meet your specs and requirements. Custom Bulk Bags prides itself on the quality and consistency of its bulk bags. For more information about our bulk bags or to get advice on the ideal design specifications, please contact us today.
___
Custom Bulk Bags is a leading South African manufacturer of woven polypropylene bags for various industries, such as mining, chemicals and food. We are able to produce over 3.5-million bulk bags per year, keeping our customers in stock at all times. Our bags adhere to the highest levels of quality as a result of our stringent in-house testing and quality control programmes.
Custom Bulk Bags holds ISO 9001 certification and we currently have a number of UN-certified designs. We are a Level 2 B-BBEE manufacturer and supplier and fall under the ownership structure of Deneb Investments Limited. For more information on our products, contact sales@custombulkbags.co.za. Follow us on Facebook, LinkedIn and Instagram for our latest news and industry insights.